Solid as Concrete—Bulkhead Installation Made Simple
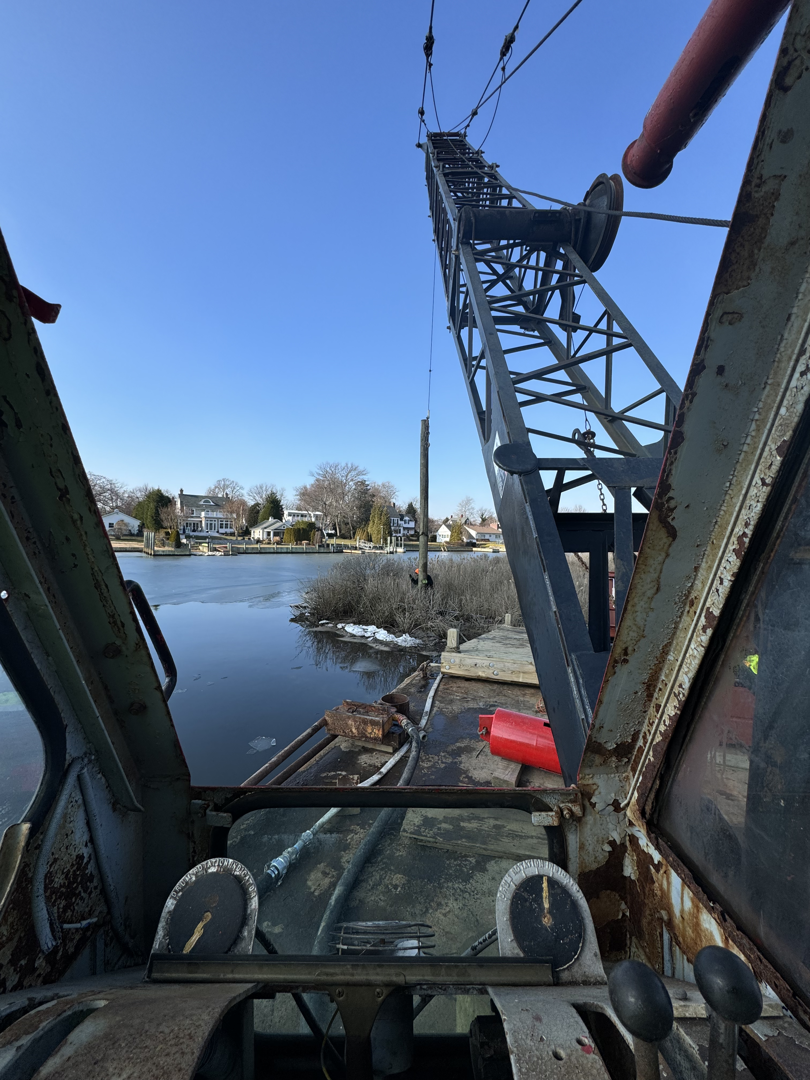
Why Concrete Bulkhead Installation Protects Your Property for Decades
Concrete bulkhead installation is the process of building a vertical retaining wall that separates your land from water while preventing soil erosion and flooding. Here's what you need to know:
Quick Installation Overview:
- Site preparation - Excavate, mark utilities, assess soil conditions
- Foundation work - Pour footing, install anchor system
- Concrete placement - Set precast units or pour in place
- Sealing - Apply gaskets and waterproof membranes
- Backfill - Compact soil, ensure proper drainage
Key Benefits:
- Durability: Lasts 50+ years with proper installation
- Strength: Uses 4000-pound concrete mix for maximum stability
- Cost-effective: Higher upfront cost but minimal maintenance
- Property value: Adds significant resale value and safety
Whether you're dealing with shoreline erosion on Long Island or need basement egress, concrete bulkheads offer the most robust solution available. Research shows that properly installed concrete bulkheads provide 21% greater shear bond strength compared to traditional materials like plywood or steel.
The installation process typically takes 1-3 days for most residential projects, with costs ranging from $5,500 for standard installations to $30,000 for advanced precast systems. Most homeowners choose professional installation due to the precision required for watertight seals and structural integrity.
Simple guide to concrete bulkhead installation:
Understanding Concrete Bulkheads: Definition, Types & Benefits
Think of a concrete bulkhead as your property's first line of defense against water damage and erosion. It's basically a vertical retaining wall that stands between your land and the water, keeping soil where it belongs while protecting your investment from Mother Nature's mood swings.
At Pearce Marine Construction, we've been building these protective barriers for waterfront properties across Long Island for years. What makes concrete bulkheads so special? They're built to last, using a 4000-psi concrete mix that can handle whatever our Northeast waters throw at them.
You've got two main options when it comes to concrete bulkhead installation: precast and poured-in-place systems. Precast units are manufactured in controlled factory conditions, then delivered and installed at your property. The quality control is excellent, and we can often complete the installation in just one day.
Poured-in-place bulkheads are built right on your property using formwork. We create the shape we need, then pour the concrete directly into place. This method gives us more flexibility for unusual shoreline configurations or tight spaces.
The engineering behind these structures uses either a gravity wall system (which relies on the concrete's weight for stability) or an anchor wall system with tie-backs for extra support in challenging soil conditions. Steel rebar reinforcement ties everything together, creating a solid barrier that won't budge.
Material | Lifespan | Maintenance | Initial Cost | Long-term Value |
---|---|---|---|---|
Concrete | 50+ years | Minimal | High | Excellent |
Wood | 10-20 years | High | Low | Poor |
Vinyl | 20-40 years | Moderate | Medium | Good |
What a Concrete Bulkhead Does for Your Property
Your concrete bulkhead works overtime to protect your Nassau or Suffolk County waterfront property. Soil retention is job number one – without proper protection, valuable land literally washes away with each tide and storm. We've seen properties lose several feet of yard in just one bad nor'easter.
Your bulkhead also acts as a flood barrier, especially when we install it with the top edge at least 2 inches above grade and pair it with proper drainage systems. This setup helps redirect water away from your foundation and keeps your basement dry during heavy rains and storm surge.
The property value boost is real and significant. Waterfront homes with quality concrete bulkheads consistently command higher prices and sell faster than properties with failing or inadequate shoreline protection.
Concrete vs. Alternative Materials—Why Go Solid
When you're weighing your options, concrete consistently wins on strength, longevity, and overall value. Wood bulkheads might look cheaper upfront, but they're constantly battling rot, insects, and marine borers that love to munch on underwater wood structures.
Vinyl bulkheads offer better durability than wood and can last 20-40 years depending on conditions. But they still can't match concrete's structural integrity, especially in areas with heavy wave action or when you need serious soil retention.
Concrete bulkheads are practically maintenance-free once properly installed. They don't rot, burn, or attract insects. They just sit there doing their job, year after year, storm after storm. The upfront investment pays for itself through decades of reliable performance without the ongoing headaches and costs that come with other materials.
Planning Your Project: Site Prep, Permits & Smart Design
Think of planning your concrete bulkhead installation like preparing for a major home renovation—the more thoughtful preparation you do upfront, the smoother everything goes. At Pearce Marine Construction, we've learned that rushing into excavation without proper planning is like building a house without blueprints.
Your first step should always be a comprehensive site survey. We examine your property's topography and conduct detailed soil analysis to understand what we're working with beneath the surface. Nassau and Suffolk County soils can vary dramatically even within the same neighborhood, so knowing your bearing capacity helps us avoid those "oh no" moments during installation.
Grading and drainage layout form the foundation of any successful bulkhead project. Water needs somewhere to go, and if you don't plan for it, it'll find its own path—usually right through your new bulkhead. We typically design a minimum 2% slope away from the structure because gravity is your friend when it comes to water management.
Before any digging begins, calling DIG SAFE at 1-888-DIG-SAFE isn't just smart—it's the law. This free service marks underground utilities, preventing you from accidentally turning your bulkhead project into an emergency utility repair.
Our rebar schedule follows strict engineering standards, typically using four rows of 5/8" rebar with highway mesh wire. For Bulkhead Design Nassau projects, we also factor in local tidal patterns and soil conditions that make Long Island's shoreline unique.
Drainage & Grading Rules You Can't Ignore
Water and concrete have a complicated relationship—they need each other to start, but water becomes the enemy over time. Poor drainage is behind most premature bulkhead failures we see, and it's completely preventable with smart planning.
The golden rule is beautifully simple: slope away from your bulkhead. Every drop of water should flow away from your structure, not toward it. We install perimeter drains that connect to daylight outfalls, giving water a clear escape route that doesn't involve your bulkhead's foundation.
Roof runoff deserves special attention because it's often overlooked. Those innocent-looking downspouts can dump hundreds of gallons directly against your bulkhead during heavy storms. We position them to divert water well away from the structure, maintaining at least 12 inches of clearance.
Material & Tool Checklist Before You Start
Professional concrete bulkhead installation requires specialized equipment that most homeowners don't have gathering dust in their garage. Here's what goes into a successful installation:
Formwork starts with Stay-Form mesh panels that create superior concrete bonding, along with traditional plywood forms for custom applications. Form ties and bracing systems hold everything in place while the concrete cures.
The concrete itself uses a 4000-pound mix for maximum strength, reinforced with steel rebar (typically 5/8" diameter) and highway mesh wire. Concrete vibrators eliminate air pockets that could weaken the structure over time.
Sealing materials include high-quality rubber gaskets, polyurethane sealant for joints, and waterproof membranes for below-grade applications. Heavy equipment includes cranes for precast unit placement, excavators for site preparation, concrete mixer trucks, and compaction equipment for proper backfill.
Concrete Bulkhead Installation Step-by-Step
The actual concrete bulkhead installation process is like conducting an orchestra – every step must happen in perfect harmony to create a structure that will protect your property for decades. Whether you're installing a precast unit or pouring in place, getting each detail right makes the difference between a bulkhead that lasts 50 years and one that fails in 10.
Excavation comes first, and it's more than just digging a hole. We excavate about 60% more soil than the bulkhead's actual volume because the structure will displace this amount when installed. Think of it like getting into a bathtub – the water level rises because your body takes up space.
Footing preparation is where the magic happens below ground. This concrete foundation must extend below the frost line and be perfectly level. In areas with questionable soil conditions, we sometimes install helical piles or other deep foundation elements. It's like building a house – you can't skimp on the foundation.
Formwork installation shapes your concrete. We prefer Stay-Form mesh panels because they provide 21% greater shear bond strength compared to traditional plywood. Plus, they stay in place after pouring, which saves time and creates a stronger final product.
Rebar placement follows strict engineering specifications. We typically use four rows of 5/8" rebar with highway mesh wire for additional strength. This steel reinforcement is what gives concrete its incredible tensile strength – concrete is great in compression but needs help with tension.
Concrete pouring happens in manageable 20-foot segments to ensure uniform curing. We use vibration tools religiously to eliminate air pockets and ensure complete consolidation around the rebar. Air pockets are like tiny time bombs that can cause failures years later.
Curing is where patience pays off. The concrete needs 7-28 days to reach full strength, depending on weather conditions. We maintain proper moisture and temperature during this critical period.
Sealing and waterproofing create the watertight barrier that protects your property. This step involves applying gaskets and sealants to all joints – it's meticulous work that determines whether your bulkhead stays dry inside.
Backfill and compaction complete the installation. We use clean, well-compacted gravel around the bulkhead. Poor compaction here can cause settling that breaks seals and compromises the entire structure.
Precast Concrete Bulkhead Installation Made Simple
Precast concrete bulkhead installation is like assembling a high-quality puzzle – the pieces are manufactured to exact specifications in a controlled factory environment, then brought to your site for precise assembly. This approach offers significant advantages over field-poured alternatives.
Factory-molded units arrive at your property with consistent quality and dimensional accuracy that's impossible to achieve with field mixing. The controlled manufacturing environment means better concrete strength, smoother finishes, and fewer defects.
Crane placement requires skilled operators who position each unit exactly according to site specifications. Our experienced crane operators work closely with ground crews to ensure proper alignment and elevation. It's precision work that looks effortless when done right.
Bolt anchoring secures precast units using high-strength bolts that thread into coil thread anchors cast into the concrete foundation. We always use thread lubricant specifically designed for this application – it ensures proper gasket sealing without damaging the threads.
One-day installation is often possible with precast units, compared to weeks for poured-in-place alternatives. This speed reduces labor costs and gets your property protection in place quickly.
The key to success lies in proper gasket installation between concrete sections. We tighten bolts to manufacturer specifications, creating a compression seal that prevents water infiltration while allowing for minor structural movement.
Poured-in-Place Bulkhead Installation Walkthrough
Poured-in-place bulkheads offer maximum customization for complex geometries or challenging site conditions. This method takes more time and skilled labor, but provides ultimate flexibility in design and construction.
Form ties maintain proper concrete thickness while withstanding the tremendous pressure of fresh concrete. These professional-grade ties break cleanly when forms are removed, leaving minimal surface defects that require finishing.
Stay-Form mesh panels provide excellent concrete bonding and remain permanently in place. The mesh openings allow visual inspection during concrete placement, ensuring complete filling of forms. This transparency literally lets us see what's happening inside the pour.
Shear bond strength improves dramatically with Stay-Form compared to traditional plywood forms. The mesh creates mechanical bonds that lock the concrete together, resulting in superior long-term performance.
Segmental pouring involves placing concrete in approximately 20-foot sections to prevent uneven setting and ensure proper curing. Control joints between segments accommodate thermal expansion and contraction – concrete moves with temperature changes, and we need to control where that movement happens.
Proper vibration eliminates air pockets and ensures complete consolidation around reinforcement. We use both internal and external vibrators to achieve optimal concrete density throughout the structure.
Ensuring a Watertight, Structurally Sound Seal
The difference between a good bulkhead and a great one comes down to sealing. Water infiltration causes more bulkhead failures than any other factor, making proper sealing absolutely critical for long-term performance.
Rubber gaskets designed specifically for concrete bulkhead applications create the primary water barrier. These gaskets must be properly sized and installed to create effective compression seals. The gasket material must withstand both concrete chemistry and environmental conditions for decades.
Polyurethane sealant provides excellent adhesion to concrete while remaining flexible over time. We apply these sealants to all joints and potential water entry points, creating redundant protection that guards against seal failure.
Compaction around the bulkhead maintains seal integrity over time. Poorly compacted soil settles and shifts during freeze-thaw cycles, breaking the seal between bulkhead and foundation. We use mechanical compaction equipment to achieve optimal soil density.
Roof runoff diversion protects the bulkhead opening from water infiltration. Proper drainage systems direct water to appropriate discharge points, protecting both the bulkhead and surrounding foundation elements.
For comprehensive waterfront protection that integrates multiple shoreline strategies, explore our Seawalls and Bulkheads services.
Budget, Timeline & Pitfalls to Avoid
Nobody enjoys budget overruns or drawn-out projects. A realistic plan for your concrete bulkhead installation prevents both.
What You’ll Spend
Cost varies by site conditions and design. Typical residential installs run $5,500–$8,000. Precast systems fall in the $20,000–$25,000 range, while intricate shoreline work can reach $30,000.
Breakdown:
- Concrete & steel: ±50 % of total
- Skilled labor: ±40 %
- Extras (excavation, inspections, disposal): ±10 %
- Excavation: $300–$500
- Foundation cutting: ≈ $475
- Local inspection fee: ≈ $472
Timeline Reality Check
Field work is fast — most projects wrap in 1–3 days once equipment rolls in. Precast installs often finish in a single shift. Add 2–4 weeks beforehand for surveys, permits and utility mark-outs. Weather matters: we won’t pour during freeze–thaw or heavy rain.
Biggest (Avoidable) Mistakes
- Rushing site prep and footing work
- Ignoring drainage or downspout placement
- Skipping gasket checks or using the wrong sealant
- Under-compacting backfill
- Starting without permits, risking stop-work orders
A quick read of our Bulkhead Builders Long Island guide can save you days and thousands of dollars. Plan well, insist on quality materials, and your bulkhead will protect your shoreline for decades.
Care, Inspection & Environmental Impact
Once your concrete bulkhead installation is complete, proper care ensures it'll protect your waterfront property for generations. We've seen well-maintained bulkheads perform flawlessly for 50+ years, while neglected ones fail in half that time.
Your bulkhead needs attention throughout the year. Spring is perfect for inspecting winter damage and clearing debris. Summer brings opportunities to monitor for settling and verify proper grading. Fall preparation involves clearing vegetation and checking for erosion. Winter monitoring focuses on ice damage prevention and ensuring proper drainage during thaw cycles.
Crack repair doesn't have to be scary. Small cracks are actually normal in concrete structures and don't necessarily mean trouble. However, any crack wider than 1/8 inch deserves professional attention. We use high-quality polyurethane sealants that stay flexible over time and bond excellently to concrete.
Preventing corrosion keeps your investment strong. While concrete itself won't corrode, the steel reinforcement inside can rust if water and oxygen reach it. This is why proper sealing matters so much. If you notice any exposed rebar, have it cleaned, treated, and recovered with appropriate patching materials.
Environmental stewardship makes good sense. Concrete bulkheads can actually benefit shoreline habitat when thoughtfully designed. They provide stable surfaces for marine organisms while protecting valuable upland areas from erosion.
We practice eco-friendly construction by using recycled concrete aggregate when possible and designing structures that work with natural water flow patterns. Native plantings above the bulkhead provide natural erosion control and help your installation blend beautifully with the landscape.
The environmental benefits extend beyond installation. A well-built concrete bulkhead lasting 50+ years means fewer replacements and less resource consumption compared to alternatives that need replacing every 10-20 years.
Research from coastal engineering studies shows that properly designed bulkheads improve local marine habitat by providing stable surfaces for organism attachment. This balance between protection and environmental responsibility is exactly what Long Island's coastal communities need.
Frequently Asked Questions about Concrete Bulkhead Installation
How long does a concrete bulkhead last?
Here's the good news: a properly installed concrete bulkhead can easily last over 50 years with minimal fuss. We've seen bulkheads from the 1970s still going strong on Long Island waterfront properties, protecting basements and preventing erosion just as well as the day they were installed.
The secret to this longevity lies in using quality materials from the start. Our 4000-pound concrete mix combined with proper steel reinforcement creates a structure that can handle decades of freeze-thaw cycles, storm surge, and everyday wear without breaking down.
But here's what really makes the difference: proper installation techniques. Bulkheads that maintain watertight seals and have adequate drainage systems consistently outlast those with shortcuts in the installation process. It's like the difference between a house built on solid foundation versus one built on sand.
The best part? Regular inspections and minor maintenance can extend that lifespan even further. We're talking about replacing a gasket here, touching up sealant there. Small investments that keep your bulkhead protecting your property for generations.
Can a homeowner install a concrete bulkhead themselves, or should a professional be hired?
We get this question a lot, and we totally understand the appeal of DIY projects. But when it comes to concrete bulkhead installation, we strongly recommend calling in the professionals. Here's why this isn't your typical weekend project.
The precision required for watertight seals is honestly pretty demanding. We're talking about creating a barrier that needs to keep water out of your basement for decades. One small mistake in the sealing process can lead to water infiltration, flooding, and thousands in damage repair.
Then there's the structural integrity aspect. Concrete bulkheads need proper foundation work, reinforcement placement, and concrete mixing that requires specialized knowledge and equipment. Most homeowners simply don't have access to cranes, concrete vibrators, or the experience to coordinate excavation with utility lines.
Professional installation also ensures you get proper permits, quality materials, and workmanship warranties. Plus, many manufacturers will void their warranties if the installation isn't done by certified contractors. When you're investing this much in protecting your property, it makes sense to do it right the first time.
What are the signs that a concrete bulkhead needs repair or replacement?
Knowing when your bulkhead needs attention can save you from major headaches down the road. Some warning signs need immediate action, while others give you time to plan for repairs.
The "call us today" signs include water infiltration into your basement or foundation areas, visible cracks wider than 1/8 inch, and any separation between bulkhead sections. If you notice soil erosion around or behind the bulkhead, or if the structure appears to be tilting or moving, these are serious structural concerns that need professional evaluation right away.
The "schedule maintenance soon" indicators are less urgent but still important. Deteriorated sealants or gaskets, exposed or rusted reinforcement, and drainage problems with standing water all signal that your bulkhead needs some attention. Even vegetation growing in joints or cracks should be addressed before it becomes a bigger problem.
The thing about bulkhead problems is they rarely get better on their own. What starts as a small crack can quickly escalate into major structural issues if left unaddressed. We recommend annual inspections for bulkheads over 20 years old or those that take a beating from severe weather conditions.
Regular professional inspections can identify problems early when repairs are less expensive and more effective. Think of it as preventive maintenance for one of your property's most important protective features.
Conclusion
When you invest in concrete bulkhead installation, you're not just building a wall—you're creating a legacy of protection that will serve your family for generations. After decades of working along Long Island's challenging shorelines, we've witnessed how the right bulkhead transforms a vulnerable waterfront into a secure, valuable asset.
The numbers speak for themselves. While wood bulkheads crumble after 10-20 years and vinyl systems show their age after two decades, a properly installed concrete bulkhead delivers 50+ years of reliable service with minimal fuss. That's not just protection—that's peace of mind during every nor'easter and hurricane season.
Your property value benefits are substantial and immediate. Quality concrete bulkheads don't just prevent costly erosion damage; they actively increase your home's marketability and resale value. Waterfront buyers recognize the difference between a property with solid shoreline protection and one that's still vulnerable to nature's forces.
The secret to long-term success lies in doing things right from the start. Professional installation using quality materials and proper techniques ensures your bulkhead performs exactly as designed. Regular maintenance keeps your investment performing at its best. Annual inspections, minor seal repairs, and proper drainage management are small efforts that preserve decades of protection.
At Pearce Marine Construction, our generational expertise means we understand Long Island's unique coastal challenges. From Nassau County's protected bays to Suffolk County's ocean-facing shores, we've built bulkheads that stand the test of time because we know what works in our local conditions.
Your shoreline deserves protection that matches your investment in your property. For comprehensive guidance on choosing the right approach for your specific situation, explore our detailed resource on Bulkhead Construction to understand all your options.
Ready to give your waterfront the solid protection it deserves? Contact us today to discuss your concrete bulkhead installation project and find how our meticulous craftsmanship delivers the quality and durability your Long Island property needs.
Contact Us
Corporate Office
Massapequa Park, NY 11762